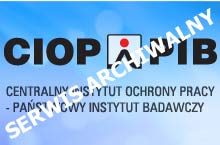  
|
|
Eliminowanie lub ograniczanie zagrożeń mechanicznych poprzez zastosowanie osłon lub innych urządzeń ochronnych przy określonej maszynie powinno być dokonane na podstawie wyników oceny ryzyka zawodowego związanego z tymi zagrożeniami w odniesieniu do badanego stanowiska pracy.
Zapobieganie to obejmuje:
- eliminowanie zagrożeń poprzez rozwiązania konstrukcyjne
- stosowanie technicznych środków ochronnych przed niewyeliminowanymi zagrożeniami mechanicznymi.
- stosowanie innych środków zmniejszających ryzyko związane z zagrożeniami mechanicznymi
Podstawowe środki zapobiegania zagrożeniom mechanicznym dostępne na stronie http://www.ciop.pl/6563.html
Pozostałe środki zmniejszające ryzyko związane z zagrożeniami mechanicznymi
|
Najczęściej stosowanymi środkami ochrony zbiorowej przed upadkiem z wysokości stanowią balustrady, natomiast najczęściej stosowanymi środkami ochrony przed wpadnięciem osób do otworów i zagłębień stanowią pokrywy. W sytuacji, gdy ze względów technologicznych np. podczas budowy budynku otwory nie mogą być zakryte pokrywami lub wówczas, gdy pokrywy są odchylone lub zdjęte to strefy niebezpieczne również powinny być wygrodzone balustradami. Balustrada składa się z poręczy umieszczonej na wysokości 1.1 m , poprzeczki umieszczonej w połowie wysokości oraz krawężnika o wysokości 0,15 m. Przykłady zastosowań balustrad przedstawiono na rys.
Bezpośrednim ingerencjom człowieka w strefy niebezpieczne zapobiega stosowanie prostych narzędzi pomocniczych przedstawionych na rysunku służących do wkładania i wyjmowania oraz wprowadzania elementów do strefy niebezpiecznej.
|
| |
Ręczne narzędzia pomocnicze |
Eliminowaniu lub ograniczaniu związanych z procesem pracy ingerencji człowieka w strefach niebezpiecznych służą przede wszystkim:
- mechanizacja i automatyzacja
- stosowanie systemów diagnozowania niesprawności
- wydłużanie okresów między wymaganymi regulacjami, smarowaniami i innymi czynnościami związanymi z obsługą techniczną
- wydłużanie okresów międzynaprawczych.
Automatyzację można na przykład realizować poprzez stosowanie robotów, manipulatorów, urządzeń przenoszących, zdmuchiwaczy. Mechanizację można na przykład realizować poprzez stosowanie ześlizgów, podajników, bębnów odwijających itp.. Należy uważać, żeby stosowanie tych urządzeń nie powodowało dalszych zagrożeń (np. pochwyceniem, zgnieceniem) między urządzeniami a częściami maszyny lub obrabianymi przedmiotami/materiałami.
Innymi środkami zmniejszającymi ryzyko związane z zagrożeniami mechanicznymi są:
- środki bezpiecznego dojść (schody, drabiny, klamry, pomosty) i dostępu (otwory) do miejsc obsługi technicznej,
- wyposażenie do łatwego przenoszenia maszyn i ich ciężkich części z zachowaniem bezpieczeństwa (np. haki, zaczepy, śruby oczkowe, rowki prowadzące dla wideł wózków podnośnikowych) ,
- środki do odłączania energii (np. rozłączniki główne zamykane na klucz) i rozpraszania energii zgromadzonej np. w sprężynach, zbiornikach pod ciśnieniem
- środkami zmniejszające skutki zdarzeń zagrażających takie jak: urządzenia do zatrzymania awaryjnego oraz środki do uwalniania i ratowania osób np. uwięzionych w maszynie,
- informowanie i ostrzeganie o zagrożeniach przy pomocy urządzeń sygnalizacji świetlnej i dźwiękowej, stosowanie barw i znaków bezpieczeństwa, piktogramów, komunikatów słownych umieszczanych bezpośrednio na maszynach i innym wyposażeniu stanowisk pracy oraz instrukcje bezpieczeństwa i higieny pracy dostępne i zrozumiałe dla pracowników,
- stosowanie przez pracowników odzieży i obuwia roboczego ograniczających sytuacje zagrożenia mechanicznego np. obcisłe kombinezony, zapięte rękawy i nogawki ograniczają pochwycenie.
Gdy omówione ww. środki nie pozwalają na osiągnięcie akceptowalnego poziomu ryzyka należy stosować środki ochronny indywidualnej. W zakresie ochrony przed zagrożeniami mechanicznymi będą to przede wszystkim środki ochrony przed upadkiem z wysokości, przed spadającymi przedmiotami, ostrymi elementami.
LITERATURA
- Bezpieczeństwo pracy i ergonomia. Red. nauk. D. Koradecka. Warszawa CIOP, 1999
- Myrcha K., Gierasimiuk J.:Zarządzanie bezpieczeństwem i higieną pracy Czynniki mechaniczne . W: Ocena ryzyka zawodowego. Podstawy metodologiczne . Pod red. W.M. Zawieski. Warszawa, CIOP 2004, s. 269-289.
- Maszyny i inne urządzenia techniczne. Środki ochrony przed zagrożeniami mechanicznymi Warszawa, CIOP 2002 – broszura wydana w wyniku projektu PHARE PL 99/IB-SO-01
- Podstawy prewencji wypadkowej, Warszawa, Praca zbiorowa, CIOP- PIB 2003
- K.M. Benczek, M. Gliński, M. Dąbrowski, H. Karski Zasady ograniczania ryzyka zawodowego podczas obróbki drewna twardego ręcznymi narzędziami zmechanizowanymi
- Bezpieczeństwo maszyn i urządzeń produkcyjnych. analiza ryzyka metody eliminacji i ograniczania ryzyka. Warszawa, CIOP 2002 – broszura wydana w wyniku projektu PHARE PL 99/IB-SO-01
- Projektowanie układów wychwytujących zanieczyszczenia, emitowane przez obrabiarki do drewna. Warszawa, CIOP 2002 – broszura wydana w wyniku projektu PHARE PL 99/IB-SO-01
- Rozporządzenie Ministra Pracy i Polityki Socjalnej z dn. 26 września 1997 r. w sprawie ogólnych przepisów bezpieczeństwa i higieny pracy. (Tekst jednolity Dz.U.2003 Nr 169, poz. 1650, zmiana Dz.U.2007 Nr 49, poz. 330)
- Rozporządzenie Ministra Gospodarki z dnia 20 grudnia 2005 r. w sprawie wymagań zasadniczych dla maszyn i elementów bezpieczeństwa (Dz. U., Nr 259, poz. 2170)– transponuje do prawa polskiego Dyrektywę 98/37/WE tzw. „maszynową”.
- Rozporządzenie Ministra Gospodarki z dnia 30 października 2002 r. w sprawie minimalnych wymagań dotyczących bezpieczeństwa i higieny pracy w zakresie użytkowania maszyn przez pracowników podczas pracy (Dz. U. Nr 191, poz. 1596 zmiana Dz. U.2003 Nr 178, poz. 1745) transponuje do prawa polskiego Dyrektywy: 89/655/EWG, 95/68/WE i 2001/45/WE.
- PN-EN-ISO12100-1:2005 Bezpieczeństwo maszyn . Pojęcia podstawowe, ogólne zasady projektowania. Część 1: Podstawowa terminologia, metodyka
- PN-EN-ISO12100-2:2005 Bezpieczeństwo maszyn Pojęcia podstawowe, ogólne zasady projektowania. Część 2: Zasady techniczne
- PN-EN 294:1994 Maszyny. Bezpieczeństwo maszyn. Odległości bezpieczeństwa uniemożliwiające sięganie kończynami górnymi do stref niebezpiecznych.
- PN-EN 349:1999 Maszyny. Bezpieczeństwo. Minimalne odstępy zapobiegające zgnieceniu.
- PN-EN 418:1999 Maszyny. Bezpieczeństwo. Wyposażenie do zatrzymywania awaryjnego, aspekty funkcjonalne. Zasady projektowania.
- PN-EN 547-1:2000 Wymiary ciała ludzkiego. Zasady określania wymiarów wymaganych dla otworów wejść i dojść w maszynach.
- PN-EN 547-2:2000 Wymiary ciała ludzkiego. Zasady określania wymiarów otworów dostępu w maszynach.
- PN-EN 547-3:2000 Wymiary ciała ludzkiego. Dane antropometryczne dla wejść i dojść oraz otworów dostępu w maszynach.
- PN-EN 563:2001 Maszyny. Bezpieczeństwo. Temperatury dotykanych powierzchni. Dane ergonomiczne do ustalenia granicznych wartości temperatury gorących powierzchni.
- PN-EN 811:1999 Maszyny. Bezpieczeństwo. Odległości bezpieczeństwa umożliwiające sięganie kończynami dolnymi do stref niebezpiecznych.
- PN-EN 953:1999 Maszyny. Bezpieczeństwo. Osłony. Ogólne wymagania dotyczące projektowania i budowy osłon stałych i ruchomych.
- PN-EN 981:2002 Maszyny. Bezpieczeństwo - System dźwiękowych i wizualnych sygnałów niebezpieczeństwa oraz sygnałów informacyjnych;
- PN-EN 1005-2:2005Maszyny. Bezpieczeństwo. Możliwości fizyczne człowieka. Część 2: Ręczne przemieszczanie maszyn i ich części;
- PN-EN 1037:2001 Maszyny. Bezpieczeństwo. Zapobieganie niespodziewanemu uruchomieniu.
- PN-EN 1050:1999 Maszyny. Bezpieczeństwo. Zasady oceny ryzyka.
- EN 1088:2001 Maszyny. Bezpieczeństwo. Urządzenia blokujące sprzężone z osłonami. Zasady projektowania i doboru.
- PN-EN 61310-1:2000 Bezpieczeństwo maszyn. Wskazywanie, oznaczanie sterowanie. Wymagania dotyczące sygnalizacji wizualnej, akustycznej i wyczuwalnej dotykiem.
- PN-EN 61310-2:2001 Bezpieczeństwo maszyn. Wskazywanie, oznaczanie i sterowanie. Wymagania dotyczące oznaczania.
- PN-EN 61310-3:2002 Bezpieczeństwo maszyn. Wskazywanie, oznaczanie i sterowanie. Wymagania dotyczące umiejscowienia i działania elementów sterowniczych
|
|
|

|
|